von Sleepy » Fr 9. Okt 2020, 08:37
Ich habe noch eine ausführlichere Vorstellung des Projektes bekommen:
ABBUC-Modulgehäuse
Oder: Etwas ungenau ist manchmal besserEs fing so bei mir an: Mit der Zeit wuchs (oder quälte mich) der Wunsch A8-Prototypen und Programme aus der Vergangenheit oder etwas Schönes, Neues auf A8-Modul zu besitzen. Atari-Module unterliegen kaum der Alterung/Abnutzung und benötigen wenig Platz. Man steckt das Modul in den Computer und schaltet den Rechner an, schon kann man sofort loslegen – hach, wie schön!
Ich bin ein Freund der ersten Serie der Atari-Module. Dies bedeutet, alte „billige“ Platinen zu kaufen und auszuschlachten, dann die Platine zu modifizieren und anschließend die benötigten Daten auf Eprom zu brennen. Platinen der Atariserien CXL, RX und Taiwan Super Cartridges lassen sich leicht modifizieren und haben fast identische Maße. Man kann sie also prima als günstige, lose Platinen nutzen. Nun wird aber noch ein Modulgehäuse benötigt, da hat mich die Erstellung eines eigenen Gehäuses gereizt. Also wie kommt das Modulgehäuse vom Hirn in die Hand?
Man braucht einiges an Software, wie 3D Modeller, Slicer und PC-Treiber für den 3D-Drucker. Die Druckdatei wird in zwei Schritten erzeugt: Das 3D-CAD-Programm erzeugt ein 3D-Modell (zum Beispiel *.stl) vom zu druckenden Objekt, der Slicer schneidet das Objekt in Ebenen, die die Wege vom Druckkopf auf dieser Ebene beschreiben und speichert diese Daten in eine Steuerdatei für den 3D-Drucker als *.gcode. Für den leichten, schnellen Einstieg ist FreeCAD sehr hilfreich, als Slicer hat sich Cura 4 bewährt. Dieses Programm kann viele 3D-Modell-Dateiformate (CAD) lesen und diverse 3D-Drucker Exportdaten (= Druckdaten *.gcode) erzeugen. Bei meinem Drucker verwende ich eine SD Card mit den Druckdaten, man kann hier vorliegende Daten im Internet nutzen und ausdrucken. Hier eine Dokumentation der Erfahrungen mit dem Projekt.
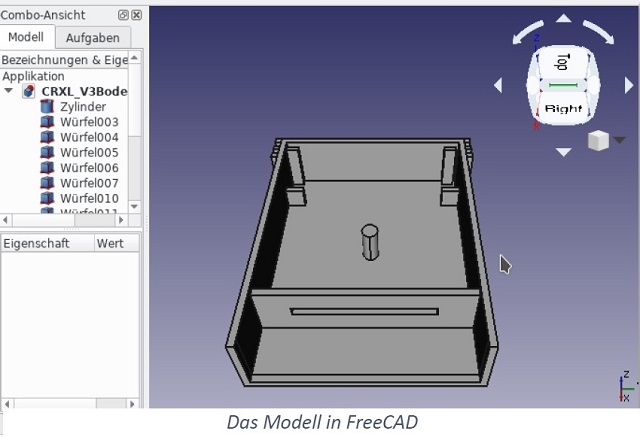
- Das Modell in FreeCAD_640.jpg (60.03 KiB) 1155-mal betrachtet
Man erfasst die Maße vom Modul, zum Beispiel Taiwan-RX-Gehäuse, dafür benötigt man unter anderem Länge, Höhe, Breite vom Gehäuse und die Position vom Zylinder auf den die Platine gesteckt und auf der richtigen Höhe gehalten wird. Weiter geht es mit dem Schlitz durch den die Platine gesteckt wird und die Aufnahme/Positionsflächen. Damit sich die Platine nicht im Modulgehäuse seitlich verschieben kann, werden wie beim Taiwan-Supercartridge links und rechts von der Platine Haltesäulen eingeplant. Der Deckel bekommt Haltepunkt-, Andruck- beziehungsweise Auflagesäulen und ein „Röhrchen“ durch das die Befestigungsschraube auf den Verschraubungspunkt im Boden geführt wird.
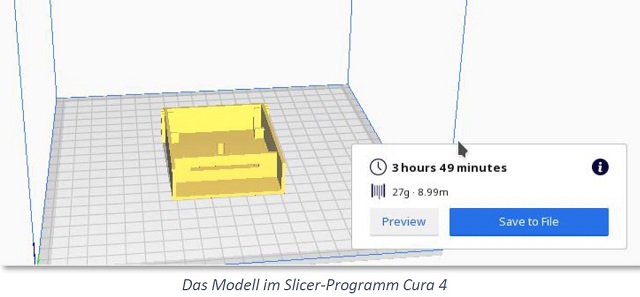
- Das Modell im Slicer-Programm Cura 4.jpg (41.55 KiB) 1155-mal betrachtet
Nun erstellt man mit den vorhandenen 3D-Formen Stück für Stück das 3D-Modell in FreeCAD. Wie man sieht, hatte ich mich auf die Formen Würfel und Zylinder + Form Verbinden/Ausschneiden beschränkt. Nachdem der Prototyp fertig war, erfolgte der erste Ausdruck. Mist, die Kontakte waren zu hoch, reichen also nicht tief genug in den Modulport. Das bedeutet für mich: Redesign.
Besonderheiten: Die Objekte werden von unten nach oben in Schichten gedruckt, somit sind „Brücken“ über Säulen eigentlich nicht möglich, der Slicer erkennt dies und erzeugt für uns passende Ebenen an solchen kritischen Stellen. Der Slicer ersetzt auch in Wänden durchgängig feste Flächen durch verstrebte Flächen und reduziert damit den Filament-Verbrauch und die Druckzeit. Der Slicer nimmt dem Designer hier viel Arbeit ab und erhöht die Möglichkeiten beim Design - das ist top! Die 3D-Drucker-Ungenauigkeiten schlagen nun zu, der Drucker druckt nur ein Vielfaches von 0,2mm somit werden 1,5mm z.B. zu 1,6mm. Wenn man das aber schon vorher weiß, verwendet man einfach 1,4 oder 1,6mm. Leider führte dies zu diversen Änderungen, da eben nur auf 0,2mm genau gedruckt wird. Zudem benötigen Röhren eine Mindestwandstärke, sonst baut beziehungsweise druckt man den schiefen Turm von Pisa nach. Da sich der Kunststoff beim Abkühlen leicht an den Ecken verzieht, durfte ich den Deckel nacharbeiten, da ich eben keine krummen Ausdrucke mag.
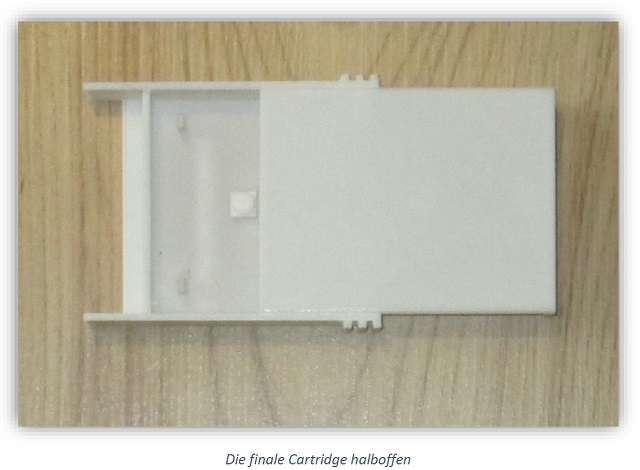
- Das finale Cartridge halboffen.jpg (70.46 KiB) 1155-mal betrachtet
Der Deckel war beim prefinalen Design ein kleiner Schwachpunkt (ein Rechteck, zirka 1-2 mm dick und nur per Schraube auf der Rückseite verschraubt). Nach der Umstellung auf das 800XL-Modulgehäuse-Design war dieser letzte kleine Mangel aber behoben (Deckel ist L-förmig, ins Gehäuse einschiebbar, wahlweise auf der Rückseite und/oder Oberseite verschraubbar). Wie bereits erwähnt, erlaubt der Slicer Aussparungen. Das war für dieses Projekt/Design sehr hilfreich. Der Boden bekam links und rechts an der Oberseite Gleitnuten, der Deckel wurde entsprechend geändert. Nun wird der Deckel in den Boden geschoben und die Schraube verhindert das Verrutschen. Die Position vom Deckel ändert sich nicht, was bei dem geringen Abstand zwischen Eprom und Deckel gut ist.
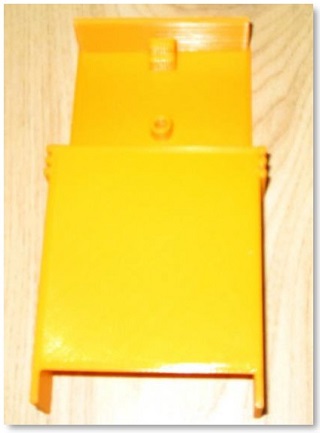
- Das finale Cartridge halboffen_2.jpg (24.9 KiB) 1155-mal betrachtet
Nur so … während ich auf der JHV an meinem Showcase döste, ist mir die Idee eingefallen. Tja, man muss manchmal weit weg, in Halbschlaf fallen - und pling, die Lösung ist gefunden. Das verwendete Filament PLA (Heißklebe-Kunststoffdraht) ist sehr spröde, sobald es etwas zu starken Druck bekommt, bricht zum Beispiel der Zylinder im Modul ab. Ebenso bricht die Nase im Gehäuse (die die Position der Platine wie bei Atari-Gehäusen fixiert) leicht ab, nur größere Flächen sind robust. Da der 3D-Drucker nicht auf Maß druckt, darf man die Seiten vom Deckel etwas abschleifen oder halt redesignen.
Filament 1,75mm, PLA weiß
Boden: 3,25 h; 27g; 9m
Deckel: 1,25h; 12g; 4,13m
Modul: 4,5h, 40g
Fazit:
Das einfache Design vom alternativen Gehäuse gab mir ungefähr 3 Tage nach dem Start des Projektes einen Prototypen in die Hand. Man muss alle Maße auf die (Un-)Genauigkeit des Druckers anpassen und alternative Designs für bessere Ergebnisse erstellen. Schwächen vom Filament sollten beim Design beachtet werden, in meinem Fall habe ich die Fixierung der Platine in den Deckel verlegt und damit gute Erfahrungen gemacht. Dem nackten unbehandelten Gehäuse sieht man die Herkunft an, jedoch mit einem schönen Finish kommt Freude auf. Ich reiche hiermit die finale 3D Dateien *.stl für den Abbuc Hardware Wettbewerb 2020 ein. Sollte dieser Beitrag zugelassen werden, dann dürfen Abbuc-Mitglieder das Design und die Daten für die nichtkommerzielle, persönliche und private Verwendung nutzen.